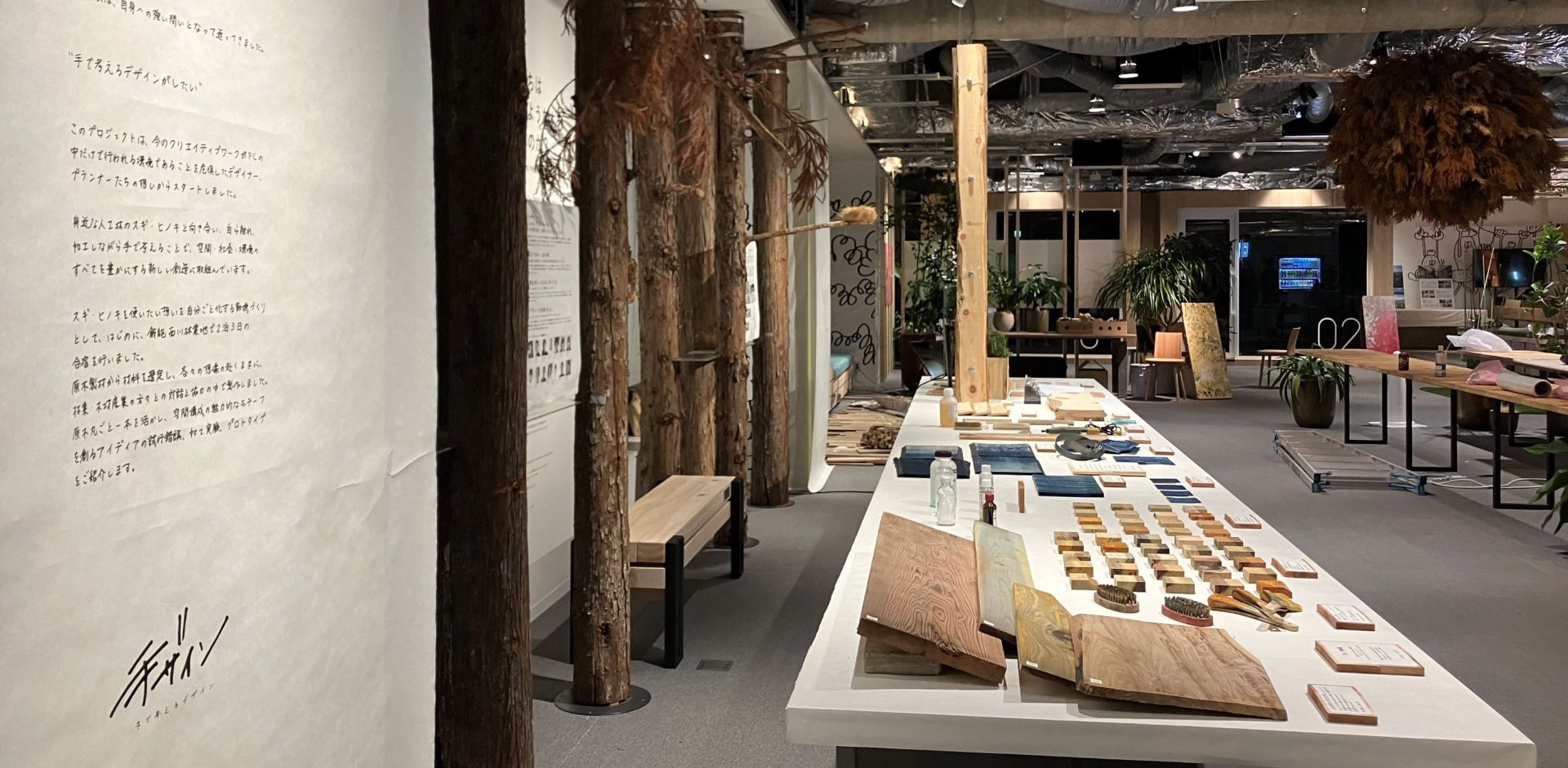
Hand-crafted design that creates a new relationship with wood
2024/04/16- text and edit by
- Local Industry Collaboration "Hand Design" Team
A new relationship with wood was born by thinking with our hands. "Hand Design" project
"NOMURA FUTURE INSIGHTS," an event to consider the future of space from the two perspectives of sustainability and digitalization and to co-create new possibilities, was held at NOMURA Co., Ltd. headquarters in Odaiba for two days on November 21st and 22nd, 2023. One of the events, "SOCIAL GOOD MARKET," presented the results of social good R&D activities conducted by over 100 members across NOMURA GROUP.
One corner that stood out in the sustainable design category was the “Hand-designed” corner.This project can be considered an evolution of the MORIMACHI Door, which was implemented in 2020.
This article is a report introducing the activities of "Te-zain," a project born out of NOMURA GROUP 's social good R&D.
Related article: The gateway to collaborative creation that nurtures forests: the "MORIMACHI Door" project
The answer may be right here
This project began with a "production area experience" where Nomura's creators visited Hanno City, Saitama Prefecture, a historic production area of Nishikawa lumber, visited forestry and wood processing businesses, walked through the forest, experienced the local culture, and learned about the feelings of the people in the production area towards wood. They learned about the various expressions of trees that have been grown over many years, how many parts are not used as lumber but are turned into fuel, and even handled offcuts that are not distributed. They asked themselves if there were ways to utilize wood as a material that they had not noticed before. And the answer was in their own hands. By being in the production area, learning about the background of wood, touching the material, and thinking with their hands while processing it, they came up with unique ideas. The results of their efforts are the current exhibition.
You will be tempted to touch the wooden surface.
For example, one experiment took the theme of "wood x catalyst" and combined wood with baking soda and wood acetic acid to see the chemical changes in color. Another involved dyeing wood with indigo and then processing it in various ways. The surface of the wood was carved to give it a tatami-like appearance. Metal powder was used to add luster. Scraps left over from the sawing process were used to create shapes. In the hands of creators, new and unexpected possibilities for wood have been born.
An experiment on chemically discoloring wood (at Kirari, a woodworking studio in Hanno, Saitama Prefecture)
The "hand-design" booth attracted a lot of interest
Inoue Hirofumi, who is leading the "Hand Design" project, Wakabayashi Tomonobu, representative of Nishikawa Rafters LLC, who assisted with coordination on the production side, and Umeda Akiko of the Future Creation Institute's Sustainable Design Lab, who has been working on this project from MORIMACHI Door, share their thoughts on the project.
R&D to help people truly love cedar and cypress
Inoue
From the perspective of a designer who works on many projects such as hotels, I honestly find it difficult to use cedar and cypress. The material is soft, and the grain of the wood inevitably has a Japanese feel. I understand the significance of using cedar and cypress, and I want to use them, but I don't think that a sense of obligation alone will lead to rich creativity. In order to truly want to use cedar and cypress as a designer, I thought it was necessary to close the distance between myself and wood. It's not enough to just see information or hear about it; I thought it was necessary to touch it with my own hands, scrape it, dye it, split it, and hit it to find the expression of the wood I want to use.
This project is an R&D project to help designers to fall in love with the materials of cedar and cypress and expand their imaginations from there. Another thing is that it is becoming common for designers these days to draw CG on a computer, order samples from manufacturers to check, and then actually assemble the product. However, if the input is the same as that of designers around the world, the output will naturally be similar. That kind of creative work will eventually be replaced by AI. I have always felt a sense of crisis about this. This time, although it takes time, we are challenging ourselves to actually move our hands, think about it, and create with our hands. By doing so, even though it is the same wood, each person will create something completely different. I think that this will become originality and become Nomura's unique style.
We named it "hand design" because the designs are done by hand. We have just started this activity. We think it is important to make this a habit and continue it, rather than doing it for each event. By doing so, we will want to use cedar and cypress not out of a sense of obligation, but because we truly love them, which will ultimately lead to the utilization of domestic timber.
Hirofumi Inoue, Designer, NOMURA Co., Ltd.
Creative Headquarters First Design Center Design Department 4 Inoue Room Room Chief
A change in mindset on the mountain side is also necessary
Wakabayashi
After the one-day production experience in July ended, the participants did not immediately go home, but instead gathered at a Chinese restaurant in front of Hanno Station and started a spontaneous discussion session. The ideas expressed at that time led to the plan for the three-day, two-night experience in October. There were two objectives. One was fieldwork to learn about the history and culture of the region at the Hanno City Museum and to see old silkworm houses* and rediscover the charm of aged wood. The other was to face the wood itself, work with our hands to process it and think about how it can be used as a material, gaining an experience that stimulates our creativity.
I have heard from designers that they are concerned about the way design is done, where everything is done on a computer, and I think I can be of help in Hanno, a timber-producing area close to the city center, where people can easily visit and experience wood. The local people say, "We want you to use more good quality wood," and "We want you to use functional pillars without knots," and of course it would be best if they could use wood, but people in the city these days don't even know about wood. I think it is first necessary for designers who use wood to experience wood and discover new charms.
At this stage, it may not be possible to utilize a large amount of wood, but I think it would be great if unused timber could be used in some way for spatial design. Even scraps that were thought to have no value can be given new value through ideas and design. I think it is also necessary for us on the mountain side to change our awareness in this regard.
* Silkworm house: a house or room for raising silkworms for sericulture.
Nishikawa Rafters LLC Representative Tomonobu Wakabayashi
I want to create "hand-made designs" that will connect to the future
Umeda
The "MORIMACHI Door" was created as an entrance where creators could meet people in the forestry and lumber industry through a production experience. We would like many people in the company to continue participating in the production experience events, so since last year, it has also been included in the training for new employees.
Related article: Learning about fairwood for a sustainable future. ~Nomura's new employee training~
However, even if their feelings changed after experiencing the production area, the actual use of wood was left to the work of each person in charge. The issue was how to create an environment that would make it easier to explore and realize wood use that utilizes the findings in the production area. After the one-day production area experience in July, the participating creators said, "I want to design with my hands," so we held a two-night, three-day experience that led to the creation of the prototype exhibited this time. Before going to Hanno, we divided into teams of two or three people and thought in advance about how we wanted to process the wood under the loose theme of "things that make up a space," and prepared materials and tools. However, after watching the actual lumbering demonstration, many ideas came to us in the process of selecting and processing various types of wood and scraps that we wanted to use.
The realization of this initiative is based on daily communication with the people in the production areas who accept and support us. We believe that designs born from such activities should be able to co-create ways of using wood that will enrich not only the completed wooden space, but also the industry and forests of the production area. While valuing both the process and the output, we would like to eventually develop the ideas born from "hand design" into our customers' business spaces and make them useful to local people, connecting them to the future of forest and space creation.
Akiko Umeda, Planner, NOMURA Co., Ltd.
Creative Headquarters Future Creation Research Institute Sustainable Design Lab
Next time, we will ask members of the "Hand Design" project about their thoughts on the exhibited works.
Text: Sho Iwasaki
[Hand-design exhibit information]
We will be exhibiting the following hand-designed items at the event "Living with Wood" being held at Tokyo Midtown Hibiya until Sunday, April 21st. Please come and visit us!
・Friday, 19th, from 6pm: Hirofumi Inoue will be taking part in the seminar (free to attend, registration required)
・First floor atrium: spatial presentation
・B1F Underground Passage: Hand-designed prototypes on display
https://www.nomurakougei.co.jp/news/page/6684/
Like this article?
- editor
-
-
Local Industry Collaboration "Hand Design" Team
Passing on the long history of forests and people to the next generation
To maintain healthy connections through our daily work